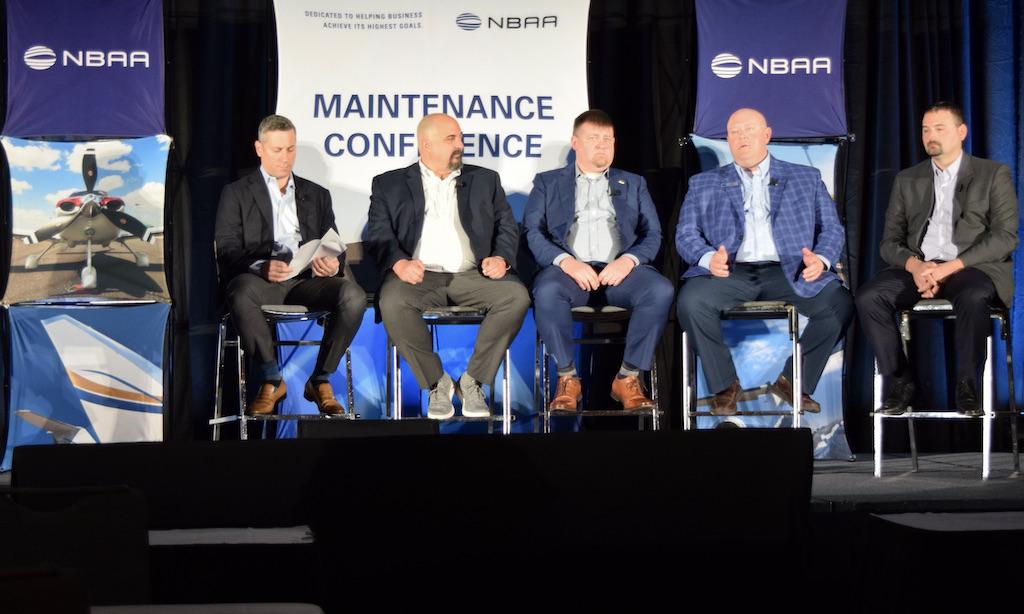
Maintenance executives discuss the state of the supply chain at the NBAA Maintenance Conference.
HARTFORD – Supply chain issues that worsened during the Covid-19 pandemic are beginning to resolve, say aircraft maintenance executives, who blame both parts and labor shortages for slowing modifications and overhauls.
There is ongoing difficulty in procuring windshields, tires and engine parts, executives said May 3 during a panel discussion at the NBAA Maintenance Conference.
The clogged parts pipeline and high demand have resulted in 8-to-12-month backlogs for some larger projects and modifications at Duncan Aviation facilities, said Ryan Huss, the MRO’s vice president of sales and marketing. The lead time to procure some engine and airframe parts can be six months.
“It really is a hangar capacity issue, a labor issue, a parts issue—all of it, not just parts,” Huss said.
Todd Hattaway, XOJET senior vice president of maintenance operations, said the charter company is planning engine work a year in advance. “It is quite the fight, but so far we’re keeping up,” he said.
Hattaway also cited obsolescence as an aggravating factor, using the example of cabin management systems.
“Some OEMs have chosen to address obsolescence and others have chosen to give you a path to buy your way out of obsolescence,” he said. “There comes a time when you’re operating a 25- or 26-year-old aircraft you have to think: is this aircraft going to do the 1,100 or 1,200 hours without full support?”
Chad Martin, Textron Aviation director of supply chain management, said shortages of raw materials and metals started in 2019 and worsened with the beginning of the Covid-19 pandemic in 2020, which caused manufacturers to reduce their workforces. Some aging workers who were laid off decided not to return when aircraft demand “exploded” in late 2020-21.
Textron Aviation has advised some of its small and medium-sized suppliers on hiring strategies and sent personnel “to run machines and bend metal to get our parts out so that we can support our customers,” he said. Last year, the airframer made more than 600 on-site visits to suppliers.
“That’s really the only way we as a general aviation industry are able to get the attention of some of these suppliers that are oftentimes answering to Boeing and Airbus and others,” Martin said.
Asked to describe the current state of supply-chain issues, Martin used a baseball analogy.
“I’d say we’re somewhere around the 7th inning stretch,” he said. “I think we’ve seen the bottom of the trough and we’re seeing signs of recovery. This time last year, if you had a CJ4, you were struggling to find brakes. We have plenty of brakes now; brakes are no longer an issue. I’d say by the end of this year we will probably be back to what we would consider our normal level of service.”